Porosity in Welding: Identifying Common Issues and Implementing Finest Practices for Prevention
Porosity in welding is a prevalent issue that typically goes unnoticed till it triggers considerable issues with the honesty of welds. In this discussion, we will explore the crucial elements adding to porosity development, analyze its damaging effects on weld efficiency, and go over the finest techniques that can be embraced to minimize porosity event in welding processes.
Common Root Causes Of Porosity
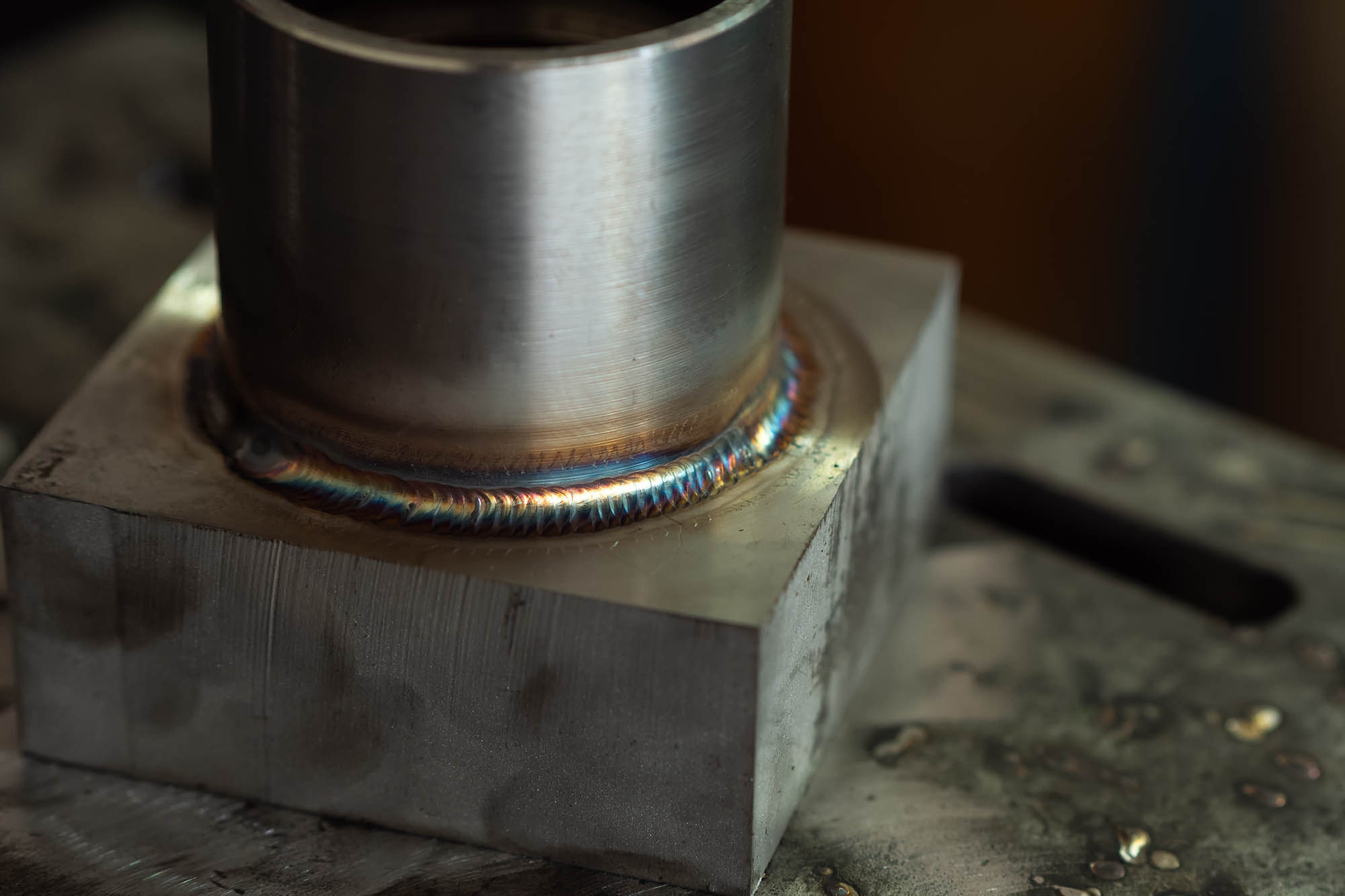
An additional constant perpetrator behind porosity is the presence of contaminants externally of the base metal, such as oil, oil, or corrosion. When these pollutants are not effectively gotten rid of prior to welding, they can evaporate and become caught in the weld, creating defects. Moreover, making use of dirty or damp filler products can present pollutants into the weld, adding to porosity issues. To reduce these typical sources of porosity, detailed cleansing of base steels, proper shielding gas choice, and adherence to optimal welding criteria are necessary techniques in attaining high-grade, porosity-free welds.
Impact of Porosity on Weld Top Quality

The existence of porosity in welding can considerably endanger the architectural stability and mechanical residential properties of bonded joints. Porosity creates spaces within the weld steel, compromising its general stamina and load-bearing capability. These gaps serve as stress and anxiety focus points, making the weld much more susceptible to fracturing and failing under applied tons. Furthermore, porosity can minimize the weld's resistance to corrosion and other environmental variables, even more lessening its durability and performance.
Welds with high porosity levels often tend to exhibit lower effect stamina and minimized capability to deform plastically before fracturing. Porosity can impede the weld's capacity to properly transfer forces, leading to view it premature weld failure and potential security threats in important structures.
Ideal Practices for Porosity Prevention
To improve the structural honesty and high quality of bonded joints, what details procedures can be applied to decrease the event of porosity during the welding process? Porosity prevention in welding is important to guarantee the stability and stamina of the last weld. One effective practice appertains cleansing of the base steel, eliminating any impurities such as corrosion, oil, paint, or moisture that could lead to gas entrapment. Making certain that the welding devices remains in good problem, with tidy consumables and proper gas flow prices, can likewise substantially decrease porosity. In addition, maintaining a secure arc and regulating the welding parameters, such as voltage, current, and travel rate, assists develop a consistent weld pool that decreases the risk of gas entrapment. Using the proper welding method for the specific material being bonded, such as changing the welding angle and weapon setting, can additionally stop porosity. Regular examination of welds and instant removal of any problems identified throughout the welding procedure are crucial techniques to avoid porosity and create top notch welds.
Value of Correct Welding Techniques
Implementing appropriate welding methods is paramount in making certain the structural stability and top quality of welded joints, developing upon the structure of reliable porosity prevention measures. Extreme warm can lead to boosted porosity due to the entrapment of gases in the weld swimming pool. In addition, using the ideal welding parameters, such as voltage, existing, and travel rate, is vital for attaining Home Page audio welds with very little porosity.
Additionally, the choice of welding procedure, whether Find Out More it be MIG, TIG, or stick welding, need to line up with the particular demands of the task to make sure optimal outcomes. Correct cleansing and prep work of the base metal, as well as choosing the ideal filler product, are additionally necessary elements of competent welding methods. By adhering to these finest techniques, welders can decrease the threat of porosity formation and produce high-quality, structurally audio welds.

Evaluating and Quality Control Measures
Quality control steps play an important role in confirming the integrity and reliability of welded joints. Evaluating treatments are necessary to discover and avoid porosity in welding, making certain the toughness and durability of the final product. Non-destructive testing approaches such as ultrasonic screening, radiographic screening, and visual evaluation are generally used to recognize possible issues like porosity. These strategies enable the analysis of weld high quality without endangering the integrity of the joint. What is Porosity.
Post-weld inspections, on the other hand, assess the final weld for any kind of flaws, including porosity, and confirm that it fulfills specified standards. Applying an extensive quality control strategy that includes thorough testing procedures and evaluations is paramount to decreasing porosity issues and ensuring the general top quality of bonded joints.
Verdict
Finally, porosity in welding can be a common issue that influences the top quality of welds. By recognizing the common causes of porosity and carrying out finest practices for avoidance, such as appropriate welding strategies and testing steps, welders can guarantee high top quality and dependable welds. It is vital to focus on prevention approaches to decrease the event of porosity and keep the integrity of welded frameworks.